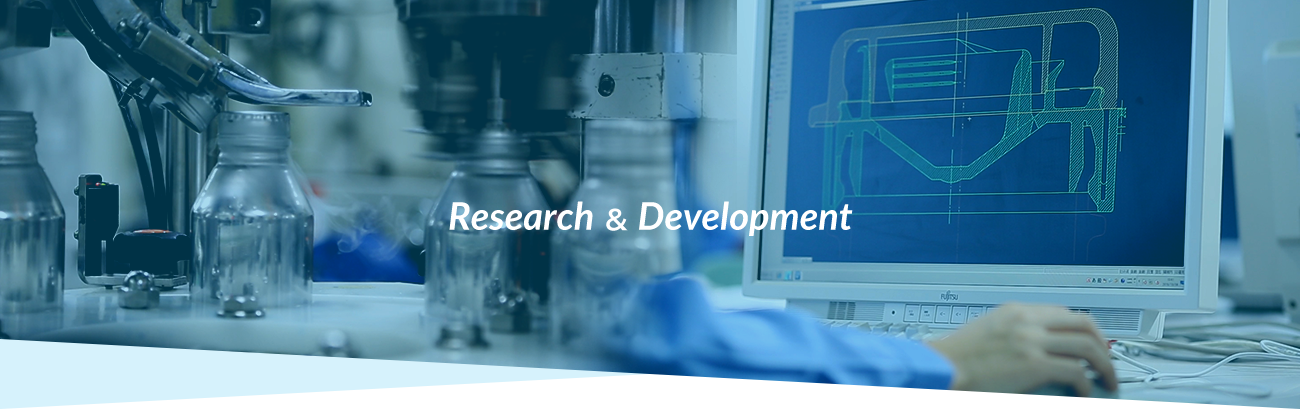
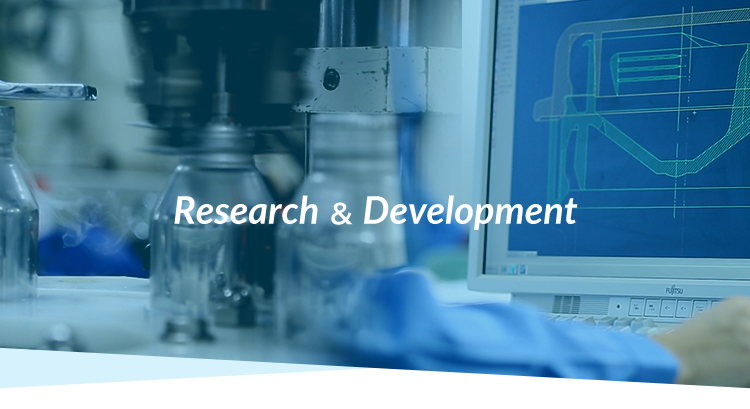
38PP-M CAN RW3A P.P.CAP
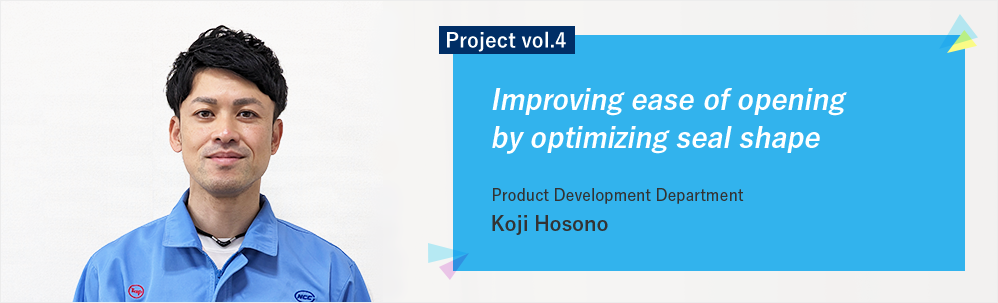
As a recent trend of the bottle can market, caps are required to possess the following performance characteristics: (1) ease of opening, (2) impact resistance, and (3) liquid spurts prevention (*1). Especially in Japan, a society with an increasingly aging population, there is strong demand for “easy-to-open” caps. Conventional P.P. caps for bottle cans are usually made by bonding a single layer of liner material to the “aluminum shell” on the top surface (which forms part of the exterior) to protect the interior. However, with this conventional adhesive method, the force required to open the cap is determined by the degree of mating force between the liner material and the bottle opening. This means reducing the mating force in pursuit of ease of opening will lower the sealing performance, resulting in a trade-off between the two.
*1. Liquid spurts: The phenomenon of liquid accumulated inside the cap spurting out when the cap is opened.
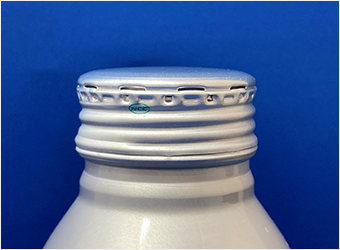
Dual layer structure to ensure both ease of opening and sealing performance
Using our proprietary liner mold technology(*2), we have created a liner structure (dual layers) that is easy to open and seals well. By making the aluminum shell and the first-layer liner non-adhesive, the bottle cap would require less force to open. Furthermore, by using a soft, heat-resistant material for the second-layer liner, we succeeded in developing a cap that is easy to open while maintaining high sealing performance. By optimizing the profile of the second-layer liner to reduce the amount of liquid accumulating inside the cap, we successfully managed to reduce liquid spurting when the cap is opened.
*2. liner mold technology: Technology to mold the liner according to a clearly defined profile
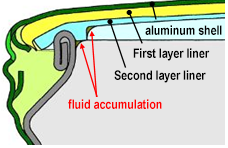
Project Review
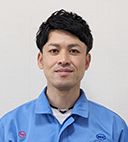
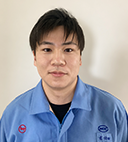
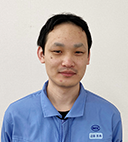