Research & Development 研究・開発
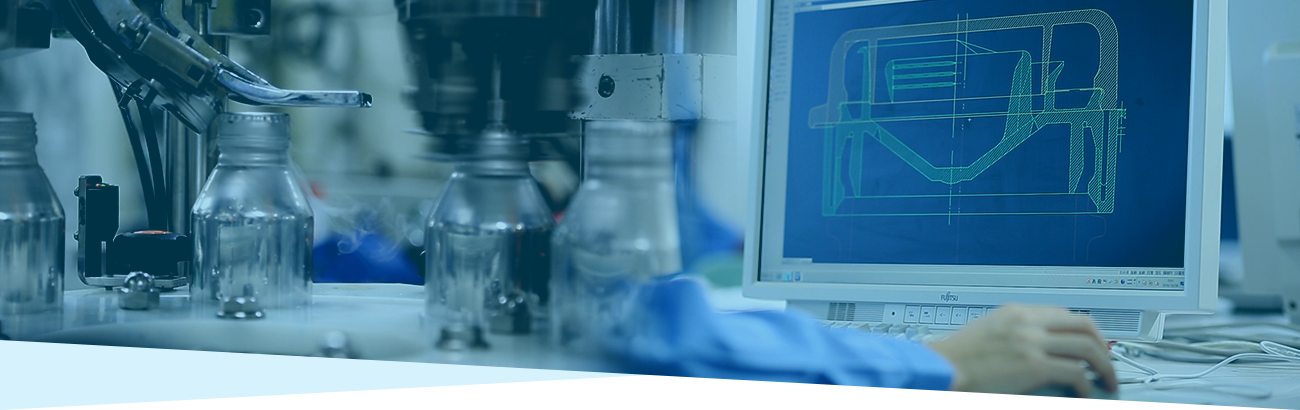
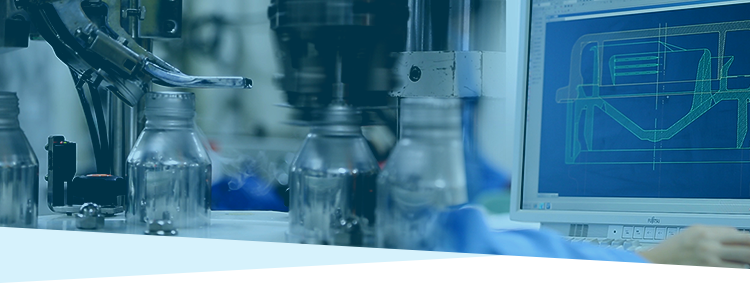
研究・開発方針
クロージャーは飲料・食品メーカー様で充填された中味を、鮮度・風味を損なうことなく、ご家庭へお届けする、いわば「タイムカプセル」のようなものです。
日本クロージャーは創業80年来培ってきた、中味を守る「密封技術」、中味の安全性を明示する「タンパーエビデント技術」、開け易さ・使い易さを追求した「易開封技術」、これら3つの技術を柱として、すべての人が安心して便利に使えるクロージャーの開発に取り組んでいます。
また以前より環境配慮型の製品開発にも力を入れてきました。金属ならびにプラスチックの使用量削減には継続的に取り組み、調味料用キャップには分別機能を付加し、さらに近年では植物由来プラスチックを用いた製品を開発し、展開を図っています。
持続可能な未来を目指し、人と社会の幸福に貢献していくために、日本クロージャーは新たな価値創造に挑戦し続けます。
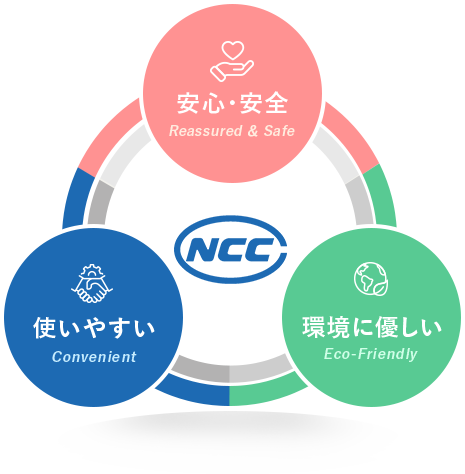